Share
Pin
Tweet
Send
Share
Send

Materials and tools:
- a drill with a cutting disc for wood 40 mm or a file for metal;
- disposable cups 0.5 l;
- pestle and mortar;
- solder;
- solder flux;
- coarse salt;
- starch;
- 5 cc syringe .;
- insulin syringe;
- heat-shrink tubing.
Making solder paste
The solder rod should be grated into a fine powder. To do this, you can use a file for metal for a long time, or use a drill with a disk for wood.

Unlike a file, its teeth are not clogged with solder. Since sawdust fly apart when sawing with a drill, it will be necessary to build a collection for them from a cut-off disposable glass. In this case, the solder itself must be in the bag in order to preserve all the powder.

It is important to feed the bar to the edge of the cutting disc at an acute angle, then it will be rubbed into finer dust. Be sure to keep your hands away from the drive.

The resulting sawdust is poured into a mortar. Coarse salt is added to them and everything is rubbed with a pestle with force. As grinding is done, a new salt needs to be added, as the crystals of the old are destroyed.


The frayed sawdust is bred in water. The salt dissolves, resulting in the remaining residue and will be crushed solder. For complete desalination, it will need to be washed a couple of times. After precipitation, the water drains.



Starch is bred in a small amount of cold water. By stirring it to weigh all particles, the solution is poured into boiling water.


A little water is added to the wet precipitate of the sawdust of solder. The mixture is mixed until the particles are weighed and poured into hot jelly. After very thorough stirring, the beaker with the combined solutions is left alone until a precipitate forms.

In a thick jelly mass, only heavy solder settles to the bottom. Its lighter small particles float to the top. Kissel is poured into another container so as not to disturb the sediment. The paste is made only of small floating particles. For their production, you will need to add more water to the jelly to reduce the concentration of starch, thereby reducing the density. This will allow the suspension to lower slightly. After the top layer of the solution without solder powder you need to drain. The procedure is repeated until the starch concentration is negligible and the precipitate begins to precipitate quickly.
After washing from starch, the precipitate of fine solder particles must be squeezed out by folding it in a napkin. The coarse dehydration mass is dried in a paper tray. This battery will take 10 minutes. The dried precipitate has clumped lumps. They can be rubbed with a finger through a napkin.

Solder flux is added to dried fine sawdust. The proportion of flux / powder is approximately 40/60 by volume. The ingredients are kneaded in a paste.
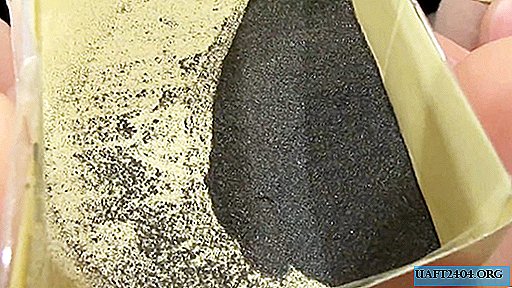



The paste is placed in a 5 mm medical syringe with an elongated piston. His nose must be connected to an insulin syringe using a heat shrink tube.

By pressing on the piston of a large syringe, you need to squeeze the paste into the insulin syringe. With this method, it will flow without the formation of pockets of air.
Subsequently, the resulting paste can be squeezed out through a thin needle of a medical syringe, or thicker from the flux. This will allow you to adjust the flow depending on the size of the soldered parts. The advantage of this paste in its property is to penetrate deeply into small capillaries. Of course, it is not so easy to do it, but the process is interesting, and soldering with it is a pleasure.




Soldering LED.


Share
Pin
Tweet
Send
Share
Send